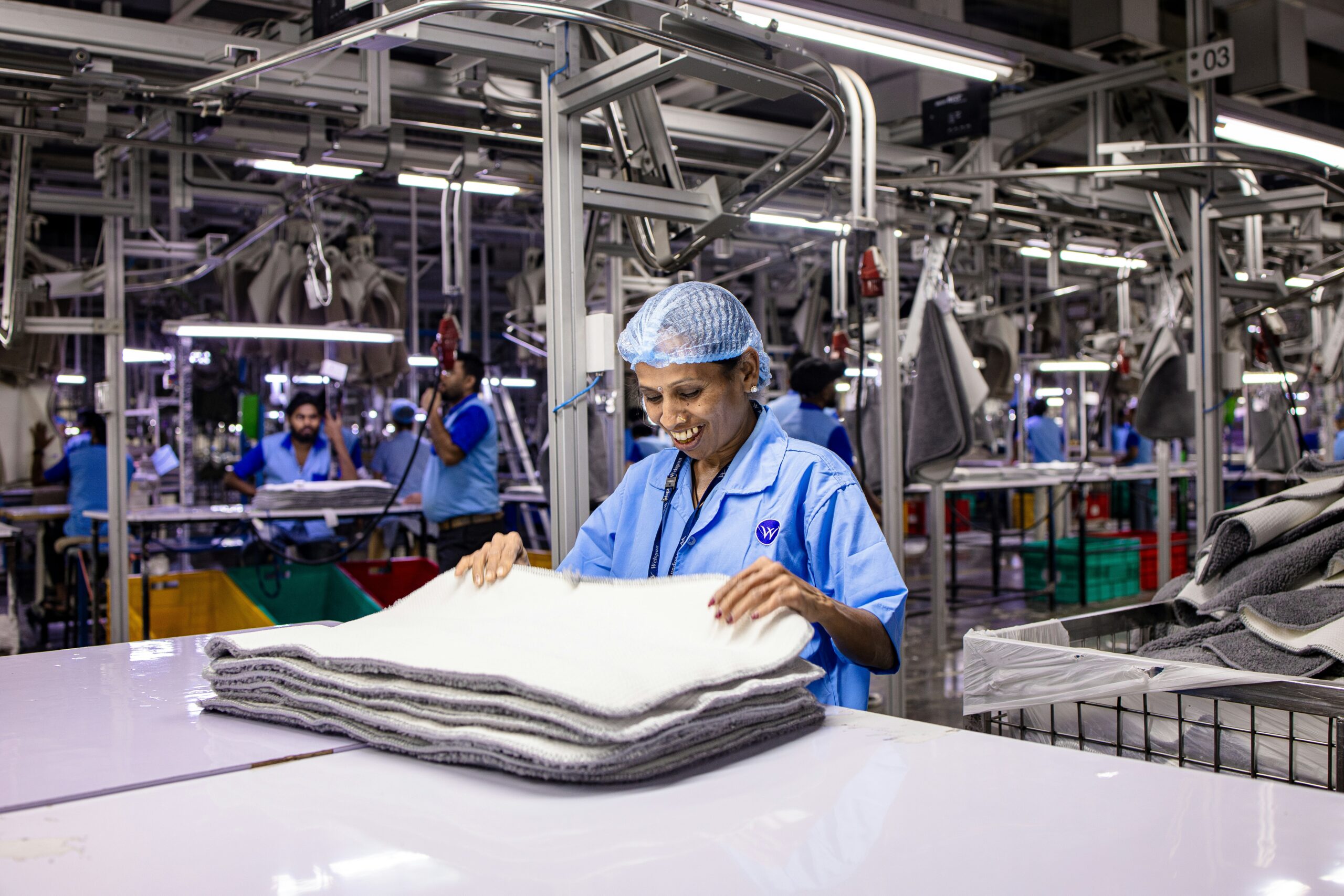
The manufacturing industry is at the cusp of a revolution, with cutting-edge technologies transforming production methods, operational efficiency, and business models. As we move into 2025, the evolution of technologies such as artificial intelligence (AI), robotics, the Internet of Things (IoT), and additive manufacturing will play a crucial role in shaping the future of manufacturing. These innovations streamline production processes and create new opportunities for sustainability, customization, and agility. This article will explore the key trends driving manufacturing forward in the coming years, highlighting how these technologies will redefine how products are made and delivered to consumers.
The Rise of Smart Manufacturing
Smart manufacturing, often called the “fourth industrial revolution,” is rapidly gaining traction as a transformative force in the manufacturing sector. By 2025, smart factories will be fully integrated environments where machines, robots, sensors, and AI systems work to optimize every aspect of the production process. These connected ecosystems will enable manufacturers to gather real-time data from every part of their operations, allowing for greater insight and decision-making.
The Internet of Things (IoT) is at the core of smart manufacturing. IoT devices are embedded in production equipment, tools, and machinery, providing continuous data streams on machine performance, environmental conditions, and product quality. AI algorithms process and analyze this data in real time, which helps predict potential failures, adjust production schedules, and improve product quality. Smart manufacturing will also lead to more adaptive production lines that can quickly switch between different products, enabling manufacturers to handle smaller batch sizes and custom orders efficiently.
Adopting smart manufacturing will lead to reduced downtime, more efficient resource use, and faster production cycles. Manufacturers can respond more flexibly to changes in demand and optimize their operations to minimize waste and costs.
Robotics and Automation: Enhancing Efficiency and Precision
Robotics has long been a significant part of manufacturing, particularly in the automotive, electronics, and heavy machinery industries. However, by 2025, robots will become even more advanced, capable of performing more complex tasks and collaborating with human workers in increasingly dynamic and safe environments. This transformation is mainly due to integrating AI and machine learning into robotic systems.
AI-powered robots are more than just automated arms that perform repetitive tasks. These robots can now learn from their environment, adapt to new challenges, and make decisions based on real-time data. For instance, robots in assembly lines can now detect defects in components, adjust production parameters, and even modify their movements to ensure precision.
Collaborative robots, or “cobots,” are designed to work side-by-side with human operators. They help alleviate the burden of physically demanding or monotonous tasks while allowing human workers to focus on more creative or complex duties. Cobots are particularly valuable in small and medium-sized manufacturing operations, where flexibility and cost-effectiveness are essential.
Fueled by robotics, automation accelerates the “lights-out” manufacturing trend, where production can continue 24/7 with minimal human intervention. This shift will significantly increase productivity, improve product consistency, and lower labor costs while reducing the risk of human error.
AI and Data Analytics: The Key to Predictive Insights and Efficiency
As manufacturing becomes more data-driven, artificial intelligence (AI) and machine learning (ML) will become central to optimizing production processes. By 2025, manufacturers will increasingly rely on AI and data analytics to gain insights into their operations, make more informed decisions, and predict future trends.
One of the most powerful applications of AI in manufacturing is predictive analytics. By analyzing large sets of historical and real-time data, AI algorithms can predict when machines will require maintenance, when production bottlenecks may occur, and how to optimize inventory levels. Predictive maintenance, powered by AI, will allow manufacturers to avoid unplanned downtime, extend the lifespan of machinery, and reduce repair costs.
AI will also improve quality control in manufacturing by automatically detecting defects during production. Advanced computer vision systems, combined with AI algorithms, will be able to inspect products with precision far beyond human capabilities. This will help manufacturers identify defects early in production, reducing waste and ensuring that only high-quality products reach consumers.
Additionally, AI-driven data analytics will be key in optimizing supply chain management. AI algorithms will analyze data from suppliers, manufacturers, and distributors to forecast demand, track materials, and optimize delivery schedules. This will lead to more efficient inventory management, reduced lead times, and a more resilient supply chain.
Additive Manufacturing: Customization and Sustainability at Scale
Additive manufacturing, or 3D printing, is another key technology set to shape the future of manufacturing. Unlike traditional manufacturing methods, which involve subtracting material from a block to create a part, additive manufacturing builds components layer by layer, allowing for more intricate and customizable designs.
By 2025, additive manufacturing will continue to grow in importance, particularly in industries that require high levels of customization, such as aerospace, healthcare, and automotive. The ability to create bespoke parts and components on demand will revolutionize production processes, enabling manufacturers to meet the increasing demand for personalized products. For instance, in the medical field, 3D printing allows for the creation of customized implants and prosthetics tailored to patients’ needs.
One of the most exciting aspects of additive manufacturing is its potential for reducing waste. Traditional manufacturing processes often result in significant material waste due to parts cutting, molding, and machining. Additive manufacturing, however, uses only the material needed to create a part, reducing waste and minimizing the environmental impact of production. Furthermore, 3D printing enables manufacturers to produce parts locally, reducing the need for long-distance transportation and decreasing carbon footprints.
The future of manufacturing technology in 2025 is bright, with innovations in AI, robotics, smart factories, and additive manufacturing driving the industry forward. These technologies will improve operational efficiency and enable manufacturers to meet the increasing demands for customization, sustainability, and agility. As manufacturing continues to evolve, adopting these advanced technologies will be essential for companies seeking to remain competitive in a rapidly changing global market. By embracing the trends shaping the future of manufacturing, businesses can unlock new levels of innovation, efficiency, and sustainability, ensuring their success in the digital age.